fastATE, True flexibility in test.
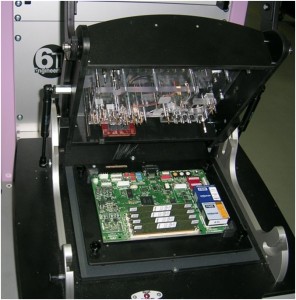
Since many years testing your printed circuit boards (PCB’s) is typically done on a bed of nails type of test fixture. The spring loaded testprobes make contact to the printed circuit board and are individually wired via switches to measurement instrumentation. A software developed test sequence will measure al the required points one by one to determine if your PCB is good or faulty. With fastATE test we are not changing this concept but enhancing this process greatly by taking out many of the typical mistaces made in the design and build of a testsolution.
Test Fixtures are used as soon as you realise that you need a reliable, reproducible and repeatable way to contact and test your PCB (printed circuit board).
Producing a PCB board involves, applying solder paste to the bare PCB using a screen printer or dispensing system. Then a P&P (Pick and Place) machine will place all components onto the fresh solder paste and finally the solder past will be reflowed in a reflow oven to solder the individual components to the PCB, So far so good.
Unfortunately during this process many thinks can go wrong, resulting in shorts, opens, missing components, lifted components, moved components, etc. therefore it is necessary to test your PCB before you build it into its final destination. To do this there are two main techniques that are used, first the optical way using manual or automatic optical inspection (AOI) or Automatic X-ray inspection (AXI). These systems can find visually many problems but have one drawback they cannot prove that the PCB really functions because there is no electrical power applied to the board. Therefore a much better approach is the electrical test being like In-circuit test (ICT) and Functional Test (FCT). In this article we will focus on ICT and FCT.
In-Circuit Test (ICT)
In circuit test is an ideal way to find so called manufacturing failures on a PCB. If you are able to get a measurement contact, test probe, on each Net of your PCB than you can find quickly and fast all shorts, opens, missing components, wrong components, misplaced components etc. Also the test result will exactly tell the operator where the missing, wrong or misplaced component is located and what the problem with it is. It also will tell where the shorts are, between which Net’s, and will show you graphically the most likely location for the short, like a track between two legs of an IC or where two Nets are really close together etc. So after production this is a reliable, fast and accurate test to find manufacturing errors.
Functional Test (FCT)
Functional test is the only way to check if the produced printed circuit board is actually functioning the way it is intended to function. The simplest way to perform a functional test (FCT) is putting the PCB in its final environment and power it up, to see if it works. This is okay if you have done an ICT test first so you are sure there are no shorts in the board that can damage, not only your unit under test (UUT), but also your entire test system.
Actual trend in testing PCB’s
These days there are two routes that companies often take, both leading to the final goal, “get as close as possible to zero defects”. Most common one is doing an optical test first, to mainly find shorts missing and misplaced components, followed by a functional test to prove the PCB is electrically working. The big advantage of doing it this way is that you do not need to invest in a bed of nails test fixture to do the optical test and it is relatively easy to make the optical test program.
But there are also a number of disadvantages of doing it this way. First is that typical an optical system is generating a lot of false failures due to simple thinks like change in colour of the silkscreen between batches, different light reflexions of the solder, bad readable imprint on the components, different results with different suppliers of components etc. etc. Therefore the best way remains an electrical ICT test providing you have good access to all or most of the Nets on the PCB.
With FCT the main problem is that if you find a problem during the FCT the time to actually find out what is causing this problem is much longer and requires a highly skilled electronics engineer, than if you know on forehand that all, by ICT tested components, are electrically the correct value, correctly placed, and that simple digital components are also working properly and placed the correct way. Even more important is also the fact that after ICT there are no shorts between Nets anywhere on the PCB anymore. If you can rule all these problems out then the FCT is only there to prove that all components work together the proper way and the board itself functions as it should do in its final destination and under “real” circumstances.
The fastATE test approach from 6TL
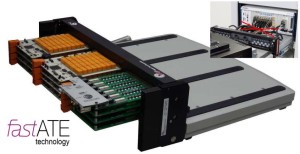
6TL engineering has developed fastATE enabling engineers to build up test systems in a flexible, modular way, using high quality Mass Interconnect interfaces and building blocks to minimize internal cabling, creating any size test solution from table top up to full in-line, in record time.
Within this fastATE concept the goal is always to make thinks more efficient, take out all recurring issues in automatic test equipment (ATE) design and capture these in one off the shelf available module. Also minimizing internal cabling inside the test system is a strong advantage of the fastATE concept. Using YAVmodule technology that are placed directly inside the mass interconnect interface we free space in the test rack behind and eliminate cabling between measurement instrumentation and mass interconnect interface minimizing issues like cross talk, signal loss, interference, additional capacitance and resistance, more complex schematics etc. etc. All these advantages lead to a more reliable and flexible test solution.
True flexibility in high volume PCB test using a combination of ICT & FCT in one solution.
6TL has already solutions ranging from small bench top testers like the highly successful 6TL-08N and 6TL-08W through table top, floor standing rack mount, to full in-line production test systems. All with one thing in common: modularity. This enables us to scale to your testing needs to match exactly your personal testing requirements. With our off-line test solutions from bench-top to floor standing test racks we have the capability to exchange and re-use the fixtures over the entire range if needed. The problem always was that moving production from an off-line test system to an in-line test solution involved always new fixturing and program debugging or even complete new program development.
New fastATE 6TL-24 combinational test system for FCT and ICT in one solution.
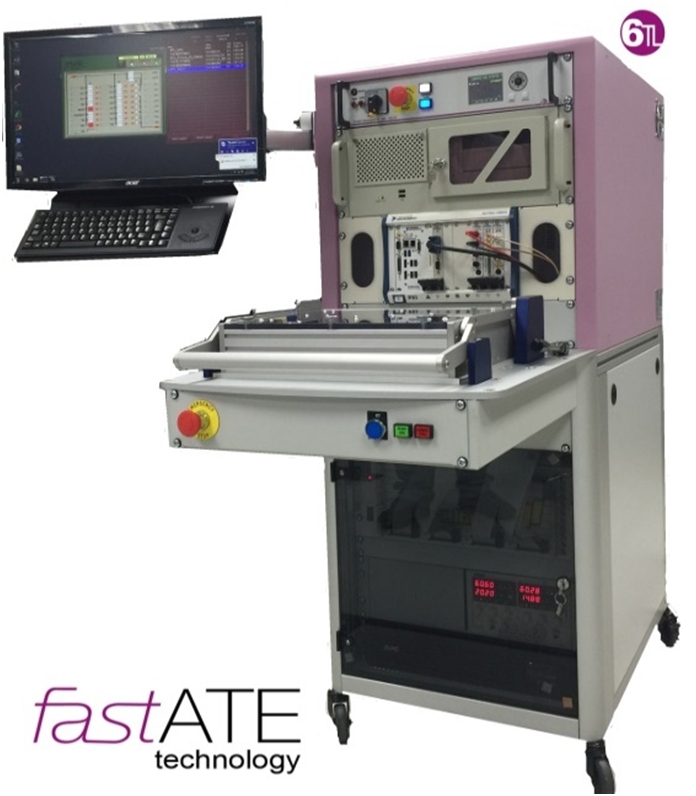
From experience we have learned that after PCB Production you need to test the UUT (Unit Under Test) to be absolutely sure that no broken UUT will leave your facility. In a PCB production environment, the best way to do this, is using ICT (In-Circuit test) because it is fast and accurately and tells you the all the shorts, opens, missing components, wrong components etc. on a component level, under one important condition that you have access to, ideally, all the Nets on the UUT.
As during PCB assembly 85-95% of the failures are production related, solder shorts, opens, missing components, tombstoning etc. you want to find these failures first.
Then after having done an ICT test you know for sure there are no wrong components, no shorts, opens and no missing components anymore so it is safe to apply electrical power to the board and the PCB should work fine. Unfortunately ICT is limited in testing the actual functionality of the board itself. Typically you want to know if the board is 100% functional or not. Therefore you also need to do a functional test (FCT).
Many people then say when they hear about this, “okay but why not only do a functional test as I have to perform this anyhow”. This off course is perfect but the problem with a functional test is that in case of a missing component or short it is much more difficult to locate the actual error on the UUT, unless maybe you have the support of a visual inspection system that replaces the ICT but this is another discussion. Also if the PCB is inside its housing, repairing a fault then requires taking it out of the housing first, which is time consuming, costly and ads additional handling, which is never good.
Combining these two tests (ICT and FCT) in one fixture and one tester would save money and would profit from the benefits of both ICT and FCT creating the best tool for testing your UUT’s
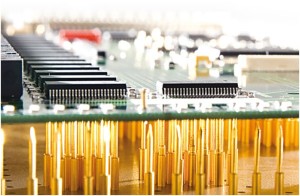
There is a though one difficulty we have to solve on the fixture side first. During the FCT you do not want all the probes used in ICT test to make contact with the board as this will influence the function off the board due to these additional contacts with wires causing antennas, additional capacitance etc.
Dual Stage Fixturing to enable combinational test.
To overcome the influence of the test probes used for ICT test while performing the FCT test you need a special feature added to the fixture where all the functional test points are using so called long travel probes and next to these, all ICT points, who use the standard conventional test probes.
In the 6TL fastATE in-line systems we have a programmable pusher or lifting system. By programming the lifter/pusher in different heights, for ICT and FCT, we can create the situation that first all probes make contact with the UUT so we can do the ICT test, and in the second stage only the long travel probes make contact to the UUT for the FCT test. This is called “Dual Stage testing”. For an off-line test system often mechanical linear push down mechanisms are used. The new 6Tl-24 has also this standard mechanical push down system enabling the use of low-cost fixture cassettes, but with the added capability of the tester to enable the two levels needed for combinational testing.
These two levels can be controlled by the test sequence.
Compatibility and interchangeability in fastATE test fixture solutions.
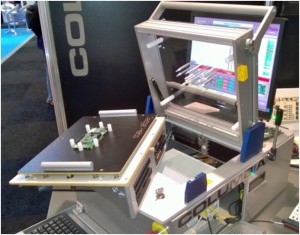
Using the same fixture and test program in your table-top, rack build or in-line test solution.
Also at Productronica 2015 we will introduce the first in-line test solution that can use the same low-cost testfixture solution and program generated for ICT and FCT as being used in our 6Tl-24 or 6TL-08 system range.
For our fastATE 6TL-08 bench top tester 6TL developed a low-cost cassette fixture system to keep fixturing cost as low possible. This same low-cost test cassette can also be used in our fastATE 6TL-24 or even in our fastATE 6TL-33 in-line test handler.
Imagine you have an in-line test system and you need to debug a new program. Today this is often done on the in-line system itself by taking it out of production and using it to develop and debug your fixture and test program. Due to the fact that the fixturing used inside an in-line handler that is capable of doing ICT is always very complicated. Due to the often large quantities of testprobes in an ICT fixture the mechanics inside the handler need to be capable of handling the force caused by these many testprobes. This results in often a strong, heavy testfixture solution that only can be used in an off line debug station using many expensive special arrangements. With the fastATE technology from 6TL you can now have a small Bench top 6TL-08 test solution to be used to debug your FCT test program and when finished take the fixture cassette and program directly to your in-line 6TL-33 test handler to start testing your high volume production.
Thanks to the fastATE 6Tl-24 we can now also use this same cassette and do the debug of your ICT and FCT combinational test program off-line and when finished take the cassette and program to the same 6TL-33 and start immediately your high-speed production. This is ideal if you use external programmers. They can now work from their own location and prepare the software and fixture in their office. When they are finished they send the program and fixture to the production facility where immediately High-speed, automatic, in-line testing can start using the same low-cost fixture and program.
Debug off fastATE test fixture off-line and simple fixture transfer to you In-line fastATE test Handler
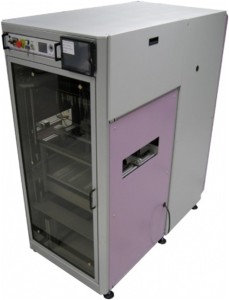
So for debugging your ICT/FCT program you do not need time of the in-line system but you can do it on an off-line station and when you finished the debug you can upload the program to the in-line system and take the fixture cassette from the off-line station and use the same in the in-line station.
Or you start with an off-line system and as soon as the production ramps up you switch to using an automatic in-line solution without having to invest in new expensive test fixtures and develop and debug new test programs.
Different optimized combinational ICT / FCT test strategies can be implemented.
To get as much UUT’s tested in one machine we need to optimize its test strategy.
For our example we assume that the ICT test takes 30 seconds and the FCT test with In System Programming (ISP), 60 seconds. For the ease of thinks we only have one single UUT and not a multi panel of multiple equal PCB’s which would even be more efficient as you will minimize on handling time.
View above the dual stage action of the 6Tl-24 |
There are several options available in the system
- Do the ICT test only
- Do the FCT test only
- Do a combinational test ICT and FCT
- Do an optimized combinational test, clever ICT and FCT
Under the optimized combinational test, the following sequence will be implemented.
- Do the ICT test (30 sec) and when it passes do the FCT test (60 sec), when both pass (90 Seconds) the UUT is tested PASS.
- Repeat this until the ICT test passes X times (5 times by default) when the ICT test has passed X times in a row we skip the ICT test and do only the FCT test. (X depends on the stability of your production process, the better you have your process under control the lower the variable X can be)
- Do only the FCT test until it fails then switch directly to the ICT test to find the fault easier by getting a much more accurate failure description and reset the value X.
- Goto step 2 (X times is needed because the failure can be caused by a wrong component for instance, in one of the feeders of your pick and place machine, if we discover repeatedly the same failure on a component during the ICT, we raise an alarm.
With the above implemented you save 30 seconds or 33% of the testing time enlarging the output capacity of your production line. And if you have your production process under control you might increase your daily output with even more than 30%.
With fastATE technology 6Tl enables engineers to build their test solutions in record time. And with the above flexibility there is always the best match to your needs.
More information on www.6tlengineering.com or write an e-mail to the author of this article, Mr. Peter van Oostrom , pvo@designedfortest.com
[button url=”https://www.testprobes.nl/romex/documents/6TL/fastATE-true-flexibility-in-test.pdf”]Download the full article in PDF format.[/button]
Peter explains 6TL’s fastATE technology at NIWeek 2015.